%20(1).png)
Company News & Events
A Window to the Future: How Starline Windows Is Leading the Way on Building Manufacturing
Find out how Starline Windows is leading the window manufacturing industry forward with innovation and digital transformation.
-1.png?width=40&name=Empowering%20Transformation%20-%20logo%20transition%20animation%20(7)-1.png)
SolidCAD 25 Feb 2025
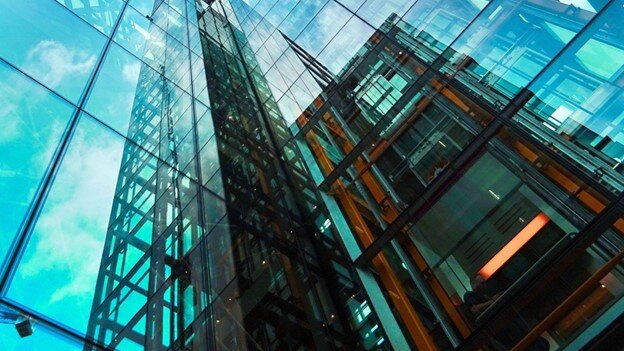
Starline Windows: A Commitment to Innovation
Ever since we started working with Starline Windows, we’ve been inspired by its commitment to innovation. The 52-year-old manufacturing company based in Surrey, BC, is not only dedicated to building better products for its end users, it’s determined to lead the entire industry forward.
According to Chief Operating Officer Lesley Noland, Starline was the first window manufacturer in Canada to go from single pane to double-sealed units to increase energy efficiency. It was also one of the first to move to powder finishes for its aluminum windows, which is more resilient and environmentally friendly than paint.
“That was in 2006,” says Noland. “We lost some customers in the process, but we continued to push the envelope, and now about 90% of the market uses powder.”
Pushing the envelope on its products has helped Starline cement its success and reputation for producing quality, high-performance windows, but it has also enabled the company to develop more efficient manufacturing processes.
“We believe that if you’re not moving forward, you’re falling behind,” Noland says. “So we’re always running. We’re raising the bar and we’re not afraid of the future.”
An Ethos of Innovation in Manufacturing
Starline is so committed to innovation and going beyond industry standards that it has been known to build its own technology to achieve its goals.
“If something doesn’t work, we build it ourselves,” Noland says. “We want to be the leaders driving change.”
The company has experimented with both software and hardware solutions to solve a variety of operational challenges.
Solving Challenges with Custom-Built Solutions
“We want to be the leaders driving change.”
– Lesley Noland, Chief Operating Officer, Starline Windows
“I remember 20 years ago, we had a storage unit with racks and carts full of long, flimsy glazing beads (the trim pieces around window glass that hold it into place),” Noland says. “Someone suggested we build a carousel to hold them all, so we literally built a 20-foot-tall ferris wheel. Today, we have about 30 of them, all different. And although state-of-the-art people now build them very officially, we built them first in our home closet.”
These days, Starline team members spend significant time researching international practices—both in and outside their industry.
“We travel all over the world and go to different trade shows,” Noland says. “We spend time in a lot of other peer groups seeing what the trailblazers are doing as well—people in the AI world, for example. We try to surround ourselves with very skillful people.”
Ten years ago, when Starline’s software couldn’t keep up with its need for efficiency, the company looked outside the North American industry for inspiration and direction.
“The rest of the world was using BIM modeling and clash detection, but North America hadn't forced it yet,” Noland says. “We figured that's where everybody was going to go, so we decided to jump in.”
Putting People Over Profits
While many companies mandate innovation as a means to greater profits, for Starline, the bottom line is not the only driving force. It’s also about creating a better experience for its people.
Automating for Worker Well-Being
In its manufacturing operations, the company has been experimenting with automated forklifts and pallet jacks to alleviate repetitive physical work that can take a toll on human bodies.
“These things are not a return on their investment at this point, but they are better for people, and they keep our systems cleaner and more stable,” Noland says. “We've been working on them for years and building them on our own.”
Noland knows these investments will eventually pay off, particularly in plant automation.
“In 20 years, I don't see the population only working until age 65 because we will be living longer. So how do you plan for these things without injuring people and their bodies?”
“Ultimately, we want to see people come out of school and be able to work. There will always be manual heavy lifting jobs, but by the age of 30, they can move into an automation role. It’s better for people over the long term.”
Robotics Eliminating Repetitive Tasks
The company is also using robotics for certain assembly processes—particularly jobs no one likes doing, such as cutting and installing insulation panels.
“That was the job you got when you were bad,” Noland laughs. “Nobody likes to do that job.”
Now, no one has to.
“Now we have a machine that does all the cutting, and then our robot arm picks up the insulation, puts it into the panel, and trims it with the saw. Nobody has to touch the insulation.”
Machines also eliminate difficult repetitive motion jobs, such as drilling holes into concrete and inserting screws.
“If you can sit there and watch the machine to make sure the screw goes in the right spot instead of having to do it yourself, that's a great thing,” Noland adds.
Overcoming Building Industry Roadblocks
While being open to new ideas can pay off, it also comes with challenges. Being an industry leader often means learning the hard way.
Finding Skilled Specialists
It’s tougher to find people with the right skills and experience.
“Finding specialists is not always easy,” Noland says.
Interoperability Challenges
Another challenge is interoperability—particularly when it comes to using industry-leading software.
“In Asia and in Europe, we see giant buildings go up in weeks rather than months because all of the planning is done virtually,” Noland says.
“I like everything to move at the speed of light, but it doesn't always work that way.”
Innovating Around Supply Chain Constraints
Supply chain constraints—such as the current glass shortage—have also propelled the company’s need to innovate.
“Because of the glass shortage, we've changed some of our products,” Noland says.
Starline has found a way to make buildings that look like they’re made of glass.
“We’re using an ACM panel in place of a piece of spandrel glass and painting it high gloss to make it look like glass,” Noland says.
“It’s also recyclable, more durable, less expensive, and more readily available at this point.”
An Eye to the Future of Window Manufacturing
What’s next for this innovator? The future is wide open, but Noland reveals the company is currently experimenting with robot arm installers.
“We have a robot that we've spent the last year designing to drill holes in concrete,” she says.
The “new toy” will eventually replace a human in a job that involves heavy labor and dangerous exposure to silica dust. But for now, it still needs heavy monitoring.
There’s no question the future will be more automated—both through robotics and AI.
“It's not replacing jobs, it's just augmenting them and making it so that the monotonous stuff isn't bogging you down all day,” Noland says.
Ultimately, by speeding up processes, the company can help get more structures built faster and cheaper.
“We're in the middle of a housing crisis,” Noland says.
“As we make the building of a project faster and easier, it will also reduce the costs.”
And that’s a win-win for everyone.
%20(2).png)
Trendings
- From Scan to Reality: How Matterport, Autodesk, ACC, and Chaos can Power the Modern Project Lifecycle
- Unleash the Power of Visual Data with RedEYE: A Revolution in Situational Awareness
- The ROI of 3D Visualization: How Stunning Visuals Improve Project Approvals and Reduce Changes
- Construction’s Biggest Questions for 2025—And How Unbound Will Answer Them
- Stop Searching, Start Working: Unlock Document Efficiency with Meridian