%20(1).png)
Industry
OpenBOM: The Platform for PDM, PLM, and Procurement - Accelerating Sales, Saving Costs, and Mitigating Risk.
Streamline product data, BOMs, and procurement with OpenBOM’s cloud-based PDM/PLM platform—eliminating silos and boosting team collaboration.

Shaya Ghanbar | Manager - Enterprise Solutions 24 Apr 2025
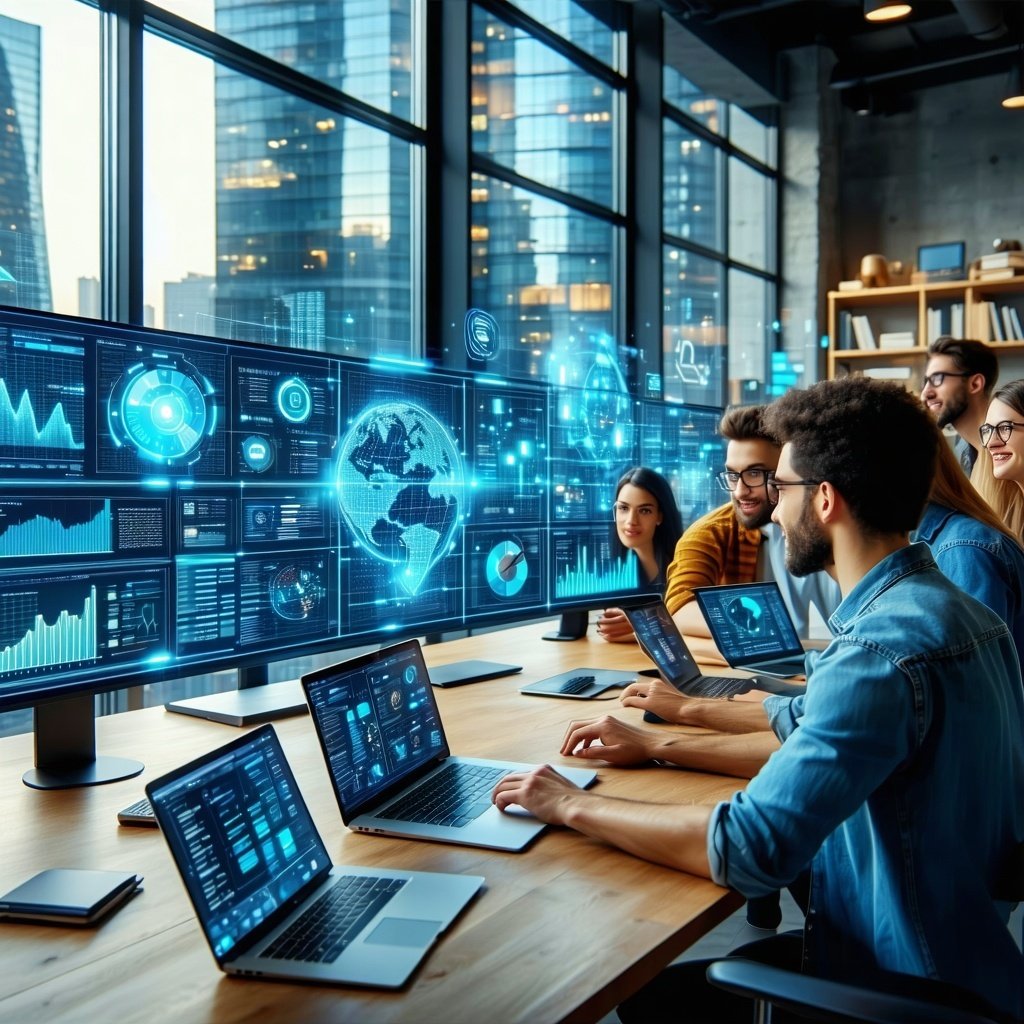
Product and manufacturing complexity raise the bar for managing product data efficiently. It is more critical today than ever. Companies depend on vast amounts of information such as design files, bills of materials (BOMs), supplier details, and procurement plans, to ensure their operations run smoothly.
However, traditional data management methods often fall short. However, legacy tools are no longer sufficient for managing today’s complex workflows—particularly when critical data is generated in Excel, stored in derivative CAD files, and shared through disconnected channels like email or Dropbox.
Usage of spreadsheets and emails, as well as outdated, disconnected systems create silos between departments, leading to inefficiencies, version control issues, and costly errors. Without a centralized and collaborative solution, teams struggle to access real-time, accurate data, slowing down decision-making and product development.
Why OpenBOM?
This is where OpenBOM steps in. Designed as a cloud-based, multi-tenant platform, OpenBOM transforms the way businesses handle product data, eliminating inefficiencies and bridging the gap between engineering, manufacturing, and procurement. By integrating key functionalities like Product Data Management (PDM), Product Lifecycle Management (PLM), inventory tracking, and procurement planning, OpenBOM ensures that all stakeholders—engineers, manufacturers, suppliers, and procurement teams—work from a single, connected source of truth. But why is this so important?
The Solution: Seamlessly Integrating and Connecting Product Data with OpenBOM
“There is a significant challenge in efficiently bringing engineering data into the business,” explains Oleg Shilovitsky, CEO and co-founder of OpenBOM. Many manufacturers still rely on outdated, disconnected systems, leading to scattered data, inefficiencies, and an increased risk of errors. Time spent retrieving and organizing information can slow down productivity and impact critical business decisions.
OpenBOM was built to eliminate these silos. By connecting teams across engineering, manufacturing, production, and maintenance, it ensures organizations have a structured, accurate, and accessible source of product data. This empowers businesses to make informed decisions, improve operational efficiency, and stay competitive in an evolving market.
What does OpenBOM do?
A list of the most important things you can do with OpenBOM:
- Bill of Materials (BOM)
- Product Planning
- Procurement Planning
- Integrated Production Management (RFQ/PO, Inventory, ERP)
- Real-time collaboration
- CAD Integration
- Change Management
- Document and Files
OpenBOM’s Collaborative Workspace transforms how teams manage product data and navigate change processes. Built as a real-time, cloud-native solution, it breaks down the silos often found in traditional PLM and PDM systems. By moving beyond local file storage, isolated databases, and fragmented email communication, OpenBOM empowers both internal teams and external stakeholders to work together seamlessly.
Teams can simultaneously access and edit Bills of Materials, item data, and design information, with every update automatically tracked and clearly attributed. This eliminates the need for manual version control or check-in/check-out systems—streamlining collaboration while preserving accountability.
The result? Accelerated decision-making, fewer errors, and a centralized, reliable source of truth that’s accessible from anywhere. With intuitive change management tools and a visual update history, OpenBOM keeps everyone aligned on what changed, when, and why—without disrupting your team’s momentum.
To support this collaborative environment, OpenBOM is also designed for flexibility. It makes it easy for you to import data from Excel, Google Sheets, and leading MCAD and ECAD systems. With quick setup and direct CAD add-ins, integrating existing data is simple. Plus, robust revision control and change management features allow you to track modifications to items, BOMs, CAD files, and drawings with confidence.
From design to production, OpenBOM helps you efficiently store, organize, and manage critical data, including inventory, vendor, and supplier details. Customizable formulas and calculation tools enable accurate cost roll-ups, while secure data-sharing capabilities support seamless collaboration across teams and external partners.
With OpenBOM, you gain a dynamic, connected, and scalable solution to streamline your product development and operational workflows.
How can OpenBOM help your business?
Product complexity, growing distribution of teams and supply chain turbulence bring many challenges to manufacturers. OpenBOM addresses these challenges with a unified, flexible platform designed to manage product data seamlessly and collaboratively. Whether you're streamlining Bills of Materials (BOMs), integrating CAD data, optimizing procurement, or enhancing team collaboration in real time, OpenBOM equips you with the tools to drive operational efficiency and confident, data-driven decisions.
Take the structured BOM, for example—OpenBOM helps manufacturers simplify production workflows and accelerate time-to-market, enabling faster responses to customer needs and unlocking new revenue opportunities. With early visibility into supply chain data, teams can proactively identify bottlenecks, refine procurement strategies, negotiate stronger supplier terms, and reduce both material and operational costs. Centralized access to current product designs and specifications also minimizes errors and rework, helping avoid delays and maintain product quality throughout the production cycle.
By harnessing these capabilities, organizations can reduce costs, manage risks more effectively, and build a more agile, resilient manufacturing operation—positioned for long-term success.
The ability to integrate with various CAD systems, such as Dassault Systèmes’s SolidWorks, Autodesk Inventor, and others, is a significant advantage. This ensures that design data flows smoothly into the BOM, eliminating manual data entry and reducing errors.
Ready to take control of your data and boost productivity? Contact SolidCAD today to learn how OpenBOM can transform your workflows and empower your business with a connected, scalable, and future-ready solution. Let’s get started!
%20(2).png)
Trendings
- Digital Transformation and Sustainability through Document Review Tools
- Optimizing for Net Zero: How Hysopt Helps Architects Design Smarter, Greener Buildings
- Optimize Building Performance with Hysopt: The Future of Energy Modeling and System Efficiency
- Connecting Design to Production: What We Learned at SolidCAD’s Digital Workflows Roundtable
- Choosing the Right Document Review Tool for Construction Teams